After melting the PTFE insulator yet another time, I’ve built another hot end. This one doesn’t use the PTFE as a stress-bearing part, but only to contain any plastic that may ooze above the top of the heater barrel.
The heater barrel is threaded into the PTFE about 0.25″, just enough to keep it aligned. The PTFE isn’t attached anywhere else, just sandwiched between the washer and the aluminum mounting plate above it.
I also made modular heater and thermistor, ala Makergear.com HeatCore. (I know a good idea when I steal it).
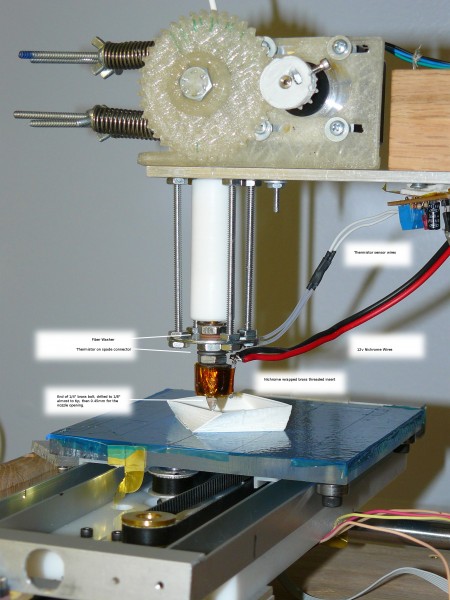
non-load-bearing PTFE
I’ve also ditched the separate nozzle, and used the brass screw as a one-part barrel+nozzle. The opening was drilled with a 0.45mm drill.
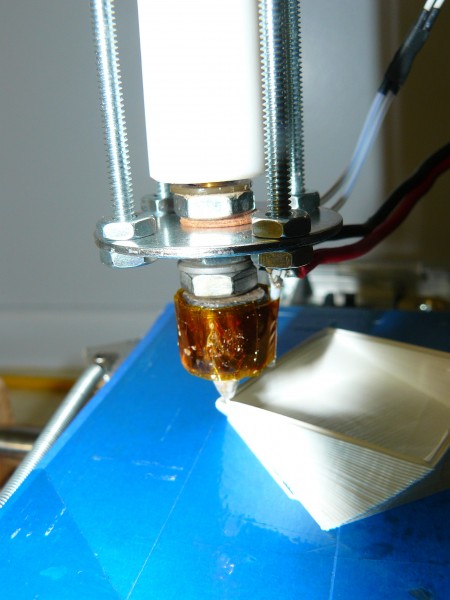
No nozzle!
Print quality has improved by a lot, and I haven’t had any problems with the feed pinch-wheel teeth stripping the filament.
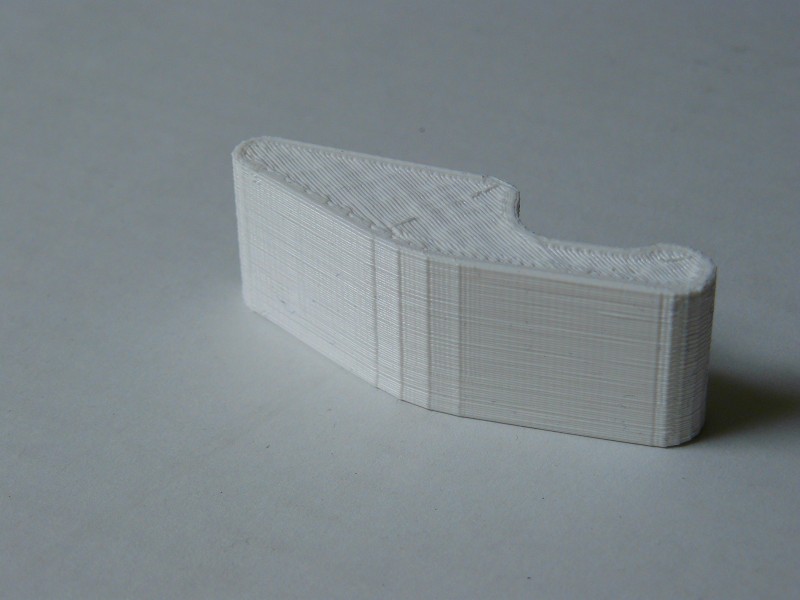
New extruder, better prints.
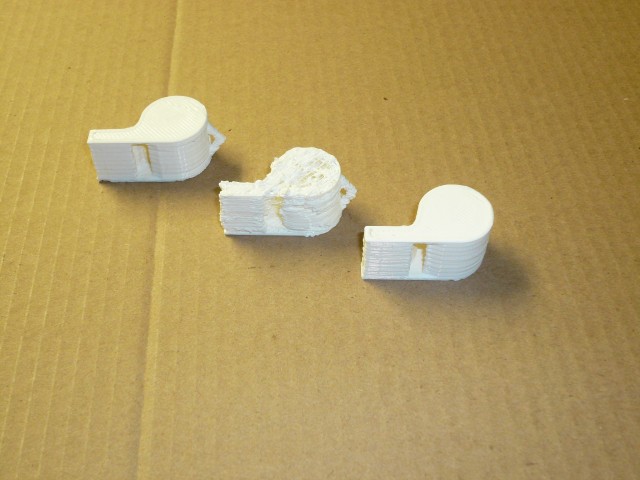
One of these things is not like the others.
After trying to do some printing with a spool of White PLA 4042D, and being unable to replicate the quality level I’d got with Natural PLA 4042D, I started to look for possible differences in the composition of the filament.
After reading the datasheets, the only documented difference is %2-%4 pigment. I’d had decent results with green & black PLA, so I wasn’t convinced that the pigment was a factor. (Although at this point I was so frustrated that I wasn’t ruling it out, either).
Read the rest of this entry »
I’ve printed so many single walled squares that I’m seeing them in my sleep.
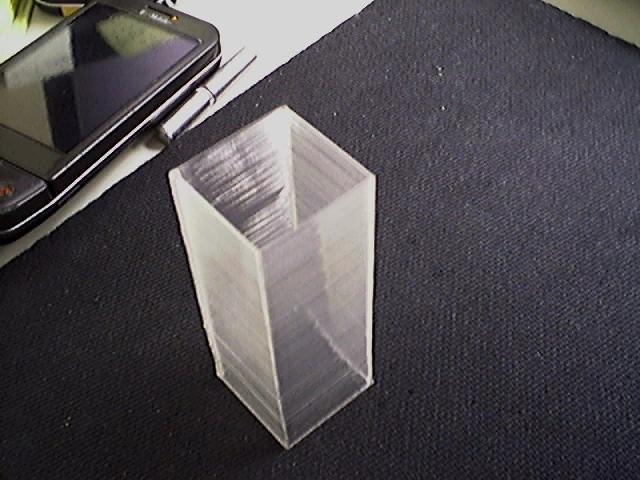
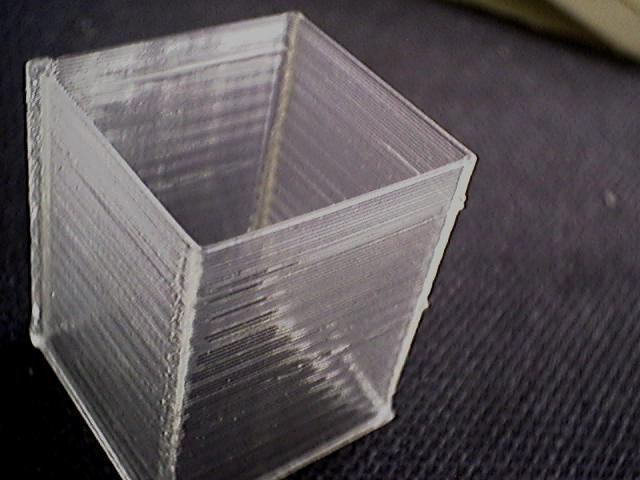
Read the rest of this entry »
Here’s a few objects I’ve printed. They came out mostly Ok, but I think I have a lot of tuning to do in Skeinforge, the software that generates the actual printing instructions. All the objects have been cleaned up with a razor, as there were some strings.
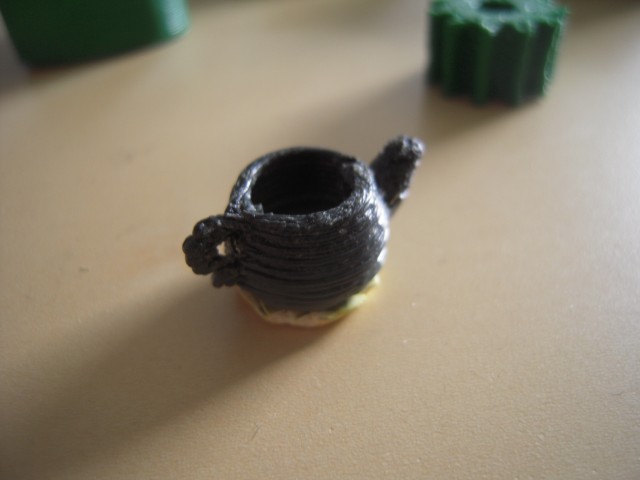
A tiny Utah Teapot
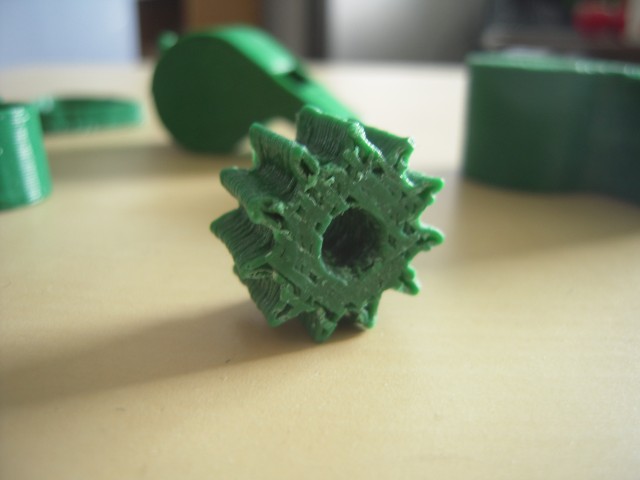
A small gear
Read the rest of this entry »
After melting the PTFE insulator on my RepStrap extruder twice, I went back to the drawing board and replaced the whole hot-end assembly.
I manually turned the new nozzle and barrel on my mini-lathe. The nichrome heater wire will wrap right around the nozzle, applying the heat as close as possible to the tip.
The heater-barrel has a reduced outer diameter, my theory being that less metal there will reduce the flow of heat up into the PTFE insulator.
Here are a few pictures.
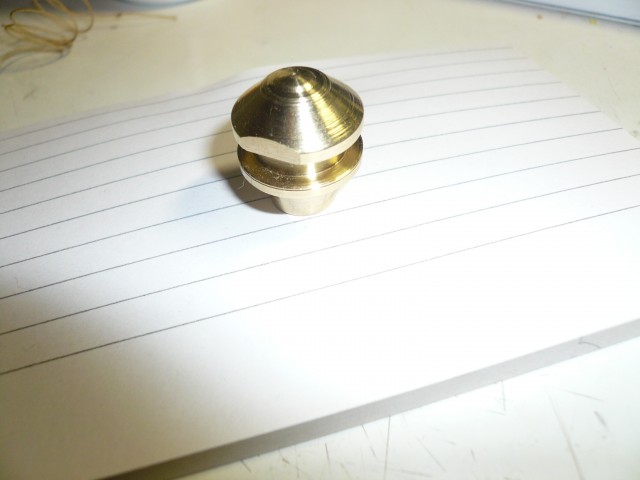
Extruder nozzle, with channel for nichrome.
Read the rest of this entry »
The RepRap is a 3D printer that builds small objects out of plastics, by squirting layers of melted plastic out of a nozzle, on to a computer-controlled moving platform. Once a single layer is made, it moves to the next layer up from the bottom, repeating this process until your object is created.
This process is called “Fused Deposition Modeling”, or “Fused Filament Fabrication”.
The end result is a strong plastic part, with a slightly ridged surface.
This is basically the same method used by the Stratasys FDM rapid prototyping machine, which costs around $30,000.
The Chicken & Egg problem of building a RepRap machine is that many of the parts are actually made using a RepRap, so if you don’t already have access to one, you’re at a disadvantage.
I’ve been working on what’s called a RepStrap, that is, it’s not exactly following the plans for a RepRap machine, but can be used to ‘bootstrap’ construction of a RepRap. The end result is the same in that you have a 3D printer, but the construction plans & materials differ.
When starting my build I had a few design goals: appearance, cost, and functionality.
Read the rest of this entry »